微波等离子清洗原理以及在微电子芯片封装工艺中的应用
微电子封装过程中产生的沾污严重影响了电子元器件的可靠性和使用寿命。研究表明,微波等离子清洗能有效增强基板的浸润性,降低芯片和基板共晶焊界面的孔隙率,同时也能清除元件表面的氧化物薄膜和有机物沾污,经过等离子清洗,其键合焊接强度和合金熔封密封性都得到提高。
封装的质量直接影响到电子元器件的可靠性和使用寿命。在微电子封装的生产过程中,由于接触、溶剂挥发、自然氧化等都可能会造成芯片、键合指或外壳焊环表面形成各种沾污。这些沾污包括环氧树脂溢出物、有机溶剂残留、焊料、金属离子、材料的氧化层等,它们都会明显影响微电子器件在生产过程中的相关工艺质量,从而降低电子元器件的可靠性和产品合格率。因此,为保证电子元器件的产品合格率和质量可靠性,必须在不破坏芯片、粘接材料和外壳的表面特性、热学特性以及电学特性的前提下,去除这些有害沾污物。
随着高科技产业的快速发展,等离子清洗适用于各种基材类型,对金属、半导体、氧化物、有机物和大多数高分子材料也能进行很好的处理,并可实现复杂结构的清洗。等离子清洗工艺中不使用任何化学溶剂,具有对环境污染小、清洗质量好等优点,在半导体制造、微电子封装、光学工业、机械与航天工业、精密仪器等领域得到了广泛的应用。
微波等离子清洗的原理
等离子体清洗
等离子体是物质常见的固态、液态、气态以外的第四态,主要由电子、正离子、自由基、光子以及其他中性粒子组成,其正负电荷总是相等的,所以称为等离子体。由于等离子体中的电子、正离子和自由基等活性粒子的存在,很容易与固体表面发生物理或化学反应,生成产物为CO2和H2O等无污染的气体,随真空泵排出,从而达到清洗的目的。
微波等离子清洗原理
常用等离子体电源激发频率有3种:激发频率40kHz的等离子体为超声等离子,发生反应为物理反应;13.56MHz等离子体为射频等离子体,发生反应为物理和化学反应;频率达到2.45GHz的等离子体为微波等离子体,离子浓度最高,发生反应为化学反应,典型的工艺是氧气或氢气等离子体工艺。用氧等离子通过化学反应,能够使非挥发性有机物变成易挥发性的CO2和水蒸气,去除沾污物,使表面清洁;用氢等离子可通过化学反应去除金属表面氧化层,清洁金属表面。
氧气等离子体其主要的形成过程如下:
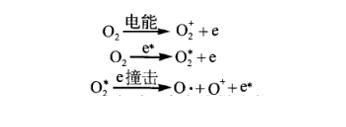
上述反应式表示氧气在微波高能电场作用下,初步生成O2阳离子和高速运动的自由电子;氧气在激发态的自由电子的轰击作用下变为激发态,生成了自由电子的过程;激发态的氧气分子在高速运动的自由电子作用下生成大量的氧自由基、氧正离子和激发态的自由电子。
用氧气等离子清洗,其中氧气主要与污染物发生氧化反应,特别是对有机沾污物清洗效果尤为明显,清洗过程反应如下:
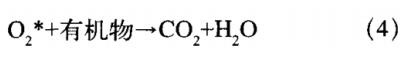
式(4)表明,处于激发态的氧气分子与有机物发生反应,生成CO2和水蒸气,对有机物溶剂沾污比较有效,具有清洗效率高、可选择性好等优点。
但是其比较明显的缺点是容易将待清洗物的金属表面或粘接材料表面氧化,因此在实际生产工艺中,常用氢等离子体将待清洗物进行还原清洗,去除金属表面氧化层,清洁金属表面。为了达到更好的效果,可在氢气中加入一定量的惰性气体氮气,将化学反应和物理反应相结合进行清洗。其过程反应如下:

式(5)表明,激发态的氢气与氧化物发生化学反应,将氧化物还原为单质和水蒸气;氮气等离子体经过物理碰撞,与H2清洗起到协同的作用。通过两种气体的清洗能有效地将待清洗物表面的氧化物去除。
微波等离子在封装工艺中的应用
等离子体清洗在半导体封装领域应用广泛。根据材料表面氧化、助焊剂残留、树脂残迹、有机物等不同沾污物的性质,选择相适应的气体,清除掉这些污染物,从而显著地改善封装可制造性、可靠性及提高成品率,表1是等离子体清洗工艺的应用。
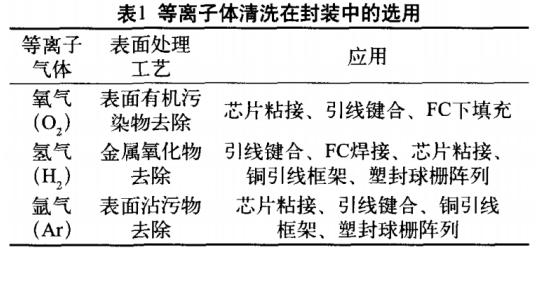
采用微波等离子清洗的实用案例。
芯片共晶前基板清洗
由于基板材料的表面存在亲水性和疏水性的特性,亲水性特性可提供良好的接触表面,共晶焊料和环氧树脂材料在其表面的流动性好、浸润性佳,可有效防止或减少焊接空洞的产生,保证高可靠的粘接和热传导能力。
微波等离子清洗能改善基板材料表面的亲水性,增强润湿性能。图1是微波等离子清洗前后的滴水试验比较,清洗后水滴在基板表面迅速扩散,接触角变小,润湿范围明显变大。
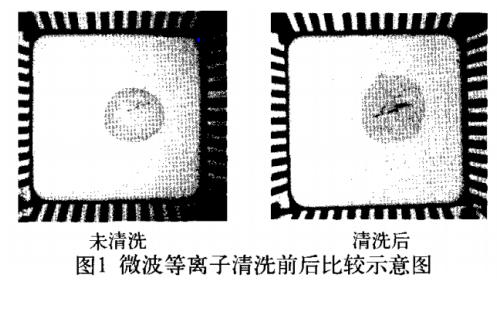
图2是芯片共晶焊接采用微波等离子清洗基板的实例。由于芯片面积较大(10mmX10mm),对材料的洁净、润湿性要求更高,焊接面孔隙控制要求小于5%,否则极易因孔隙的应力过大导致芯片碎裂或裂纹而使器件失效。基板不清洗直接共晶芯片,x射线检查焊接面孔隙多且个别孔隙尺寸大,如图2(a)所示;基板采用微波等离子清洗后,x射线检查芯片焊接Ifd4L隙少而小,如图2(b)所示。实验表明,经微波等离(-ifi洗基板后,共晶焊料流淌性好、润湿性强,焊接面孔隙率降低。
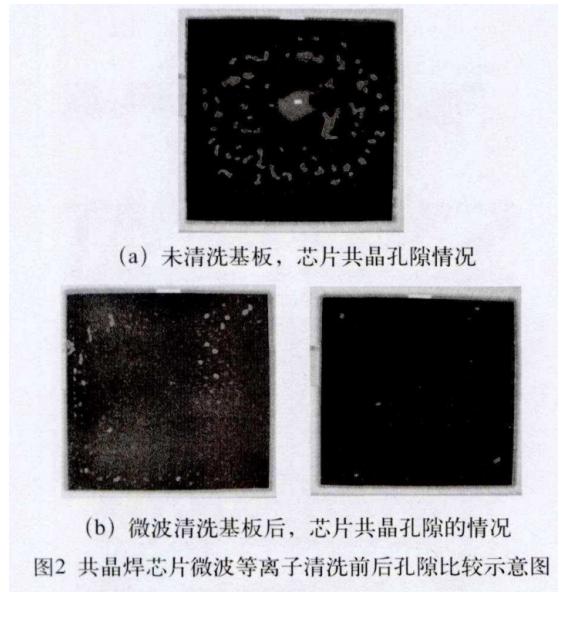
银浆有机物沾污的清洗
采用银浆粘接芯片工艺,由于银浆材料的基体树脂及材料中或多或少存在着有机溶剂及其他介质,往银浆分配后由于基板表面的亲水性,树脂扩散造成引线指区域沾污,或在固化过程中有机溶剂挥发,部分挥发物将沉积于电路表面,造成芯片、键合指或焊环表面的微量沾污。为去除有机溶剂的沾污,需任装片同化后、引线键合前采用微波等离子清洗。
图3(a)所示为导电胶粘接芯片、电路固化后有机溶剂扩散沾污键合指现象。为提高键合焊接的可靠性,采用O2等离体清洗沾污的有机溶剂。图3(b)所示为O2等离体微波清洗后的电路照片,由图中可知,微波等离子清洗之后,外壳引线指上沾污的溶剂已经去除,其颜色也恢复正常。
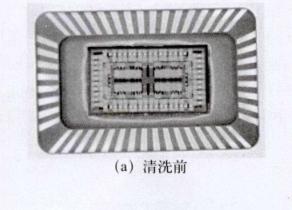
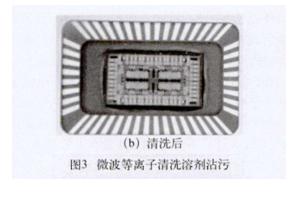
键合前清洗优化引线键合
为了研究等离子清洗对键合引线和键合指焊接强度的影响,取一只贴片后的电路,先用O2等离子清洗10min后再用N2/H2清洗10min,然后进行引线键合,之后做球形焊点的剪切强度测试。图5N示为用微波等离子清洗和未清洗的电路的引线键合强度对比图。
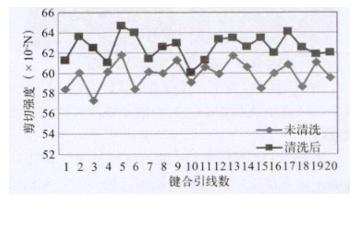
由图5可以看出,用微波等离子清洗过的电路的键合引线焊接强度好于未清洗的电路。这主要是因为清洗能够清除键合指镀金层表面的微小污物,减小镀金层表面浸润角,有效改善焊接面浸润性,增强焊接材料的互融,从而有效地增强引线焊接强度。
图6(a)所示为电阻贴片固化后表面电镀金属化层发红变色,导致引线键合可焊性差。经过O2等离子和N2/H2,等离子清洗后发红现象去除,恢复正常颜色,如图6(b)所示,满足了键合工艺要求。
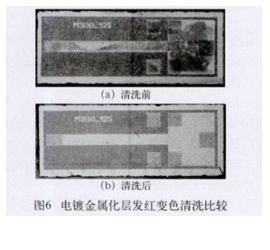
封帽前清洗优化焊接面盖板封帽作为电路陶瓷封装工艺中的后道关键工序,其密封性以及盖板和焊环的焊接强度直接影响电路的可靠性和使用寿命。取两只焊环表面有微量沽污的电路,一只用N2/H2,等离子体清洗20min,另一只不作清洗,在同样的工艺条件下进行合金封帽,最后用x射线检测焊接面焊接情况。图7所示为封帽前后的图片和x射线图像。
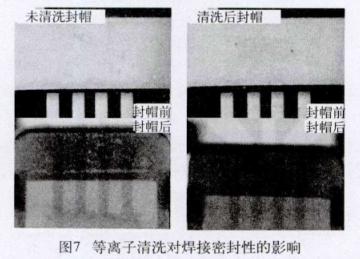
由图7中可以看出,焊环有同样轻微沾污的两只电路,经过清洗封帽的密封面的孔隙率要比未清洗的要好。
图8是焊环表面斑点状的有机物沽污,采用O2等离子体可清除掉,提高了密封焊接面的有效焊接面,减少孔隙的产生。
在陶瓷外壳封装工艺过程中,合金焊料和胶在高温条件下固化后,部分外壳镀金层质量存在不良,经高温后金层表面出现氧化变色,焊环、键合指或电镀金PAD表面氧化,导致润湿性差,影响后续的焊接可靠性。图9是经高温后焊环表面氧化,采用N2/H2,等离子清洗20min后,有效去除了氧化物,密封焊接后X射线检测焊接面润湿完好,无孔隙产生。
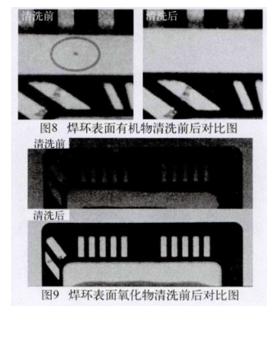
FC焊接前和下填充前的清洗
在芯片倒装前,对芯片和基板进行微波等离子清洗,清除掉金属表面微量氧化物和有机沾污,提高材料表面活性再进行倒装焊,有效地防止或减少焊接面孔隙,提高焊接强度。倒装焊接时应用到助焊剂,焊接后需采用清洗剂来清洗助焊剂。清洗后会有微量有机物残留,在下填充前采用O2和N2/H2,等离子体清洗,去除有机溶剂残留,可增加下填充料的流淌性,减小填充料孔隙、分层,提高产品可靠性。
结论:
1.等离子清洗基板能够降低芯片共晶焊产生的孔隙率。
2.等离子清洗在一定程度上能够有效清除在封装工艺过程中由于溶剂挥发、氧化物等产生的沾污。
3.贴片后的电路经过微波等离子清洗处理后,其键合引线焊接强度较未清洗的电路增强。
4.在封帽工艺中,微波等离子清洗电路能提高盖板和焊环的焊接密封性,增强其焊接强度和可靠性。