基本上任何前照灯都会应用胶粘,来满足配光镜与壳体间防漏的需求,汽车大灯对此要求更高。为确保汽车车灯的长期使用寿命,必须对它们进行有效保护,防止水分进入。在粘接由聚丙烯 (PP) 和聚碳酸酯 (PC) 制成的前照灯和尾灯时,粘合剂必须具有优异的密封性,并可提供可靠粘接。使用常压低温等离子体表面处理技术进行精确的局部预处理可将所有关键区域中的非极性材料活化,提高胶水的黏附性能,从而确保车灯的可靠粘接和长期密封。
汽车大灯
等离子清洗机表面处理提高粘接能力其在材料表面的形态得到了微观改变,低温
等离子表面处理机在处理金属材料后,能使材料表面的附着力达到62达因以上,能满足各种粘接、喷涂,印刷等工艺,同时达到了除静电的作用。
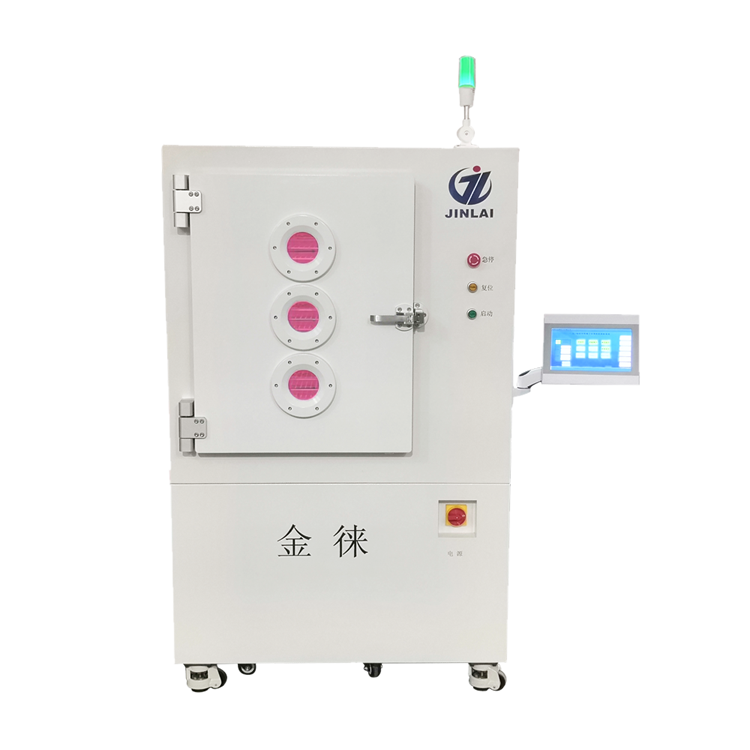
EPDM 车门密封条起到两个重要作用:防风雨,并可降低汽车内部所能感觉到的噪音水平。汽车车门密封条需要使用特殊表面涂层,以确保污物颗粒不会粘附在上面。但是,在挤出工艺中喷涂功能性涂层(减摩或植绒涂层)并不是件容易的工作。
过去,必须通过回转钢丝刷来连续对EPDM胶条进行打磨处理,这是工艺稳定性很差的加工过程。
作为一项被汽车工业迅速接受的新技术,对EPDM胶条进行金徕等离子预处理具有独特的工艺优点:
- 废品率降低,生产效率高
- 可通过等离子控制系统进行100%工艺监控
- 可靠的系统技术(全天候运行),设备可利用率高 (>99.5%)
- 调整迅速:可相对于胶条的几何尺寸,快速地可重复再现地调整等离子体喷枪的位置
随着汽车行业的不断发展,其对汽车各方面性能要求也越来越高。汽车发动机的点火系统主要由点火线圈和火花塞组成,点火系统的性能一定程度上会对动力造成影响,更换点火线圈或高性能点火线圈可以一定程度上提升动力,最明显的效果是提升行驶过程中的中低速扭矩。点火线圈做到喷油安全燃烧,充分发挥每一滴油的燃烧效率,减少或消除发动机的共振,实现增强动力、节能环保、降低油耗、清除积碳、减少排放等诸多功能。进而更好的保护发动机,延长发动机的寿命。
要使点火线圈充分发挥它的作用,其质量可靠度、使用寿命等要求就必须达到标准,但是目前的点火线圈生产工艺尚存在很大的问题。点火线圈骨架外浇筑环氧树脂后,由于骨架在出模具前表面含大量的挥发性油污,导致骨架与环氧树脂结合面沾合不牢固,成品使用中,点火瞬间温度升高,会在结合面微小的缝隙中产生气泡,损坏点火线圈,严重的还会发生爆炸现象。
点火线圈骨架使用
等离子表面处理后,不仅可去除表面的难挥发性油污,大大提高骨架表面活性,而且能提高骨架与环氧树脂的粘合强度。这样一来点火线圈在生产过程中各方面性能才能得到明显改善,也大大提高了可靠度和使用寿命。